(4)

图3 弹性阶段的应力分析Fig.3 Stress analysis in elastic phase
在接触圆外(r>a),z=0的硅片表面应力场的极坐标表达式为:
(5)
在硅片表面以下(z<0)沿z轴的应力分布可认为是在半径r上的环形集中力,即:
(6)
同时,主剪切应力τ1的分布可以表示为:
τ1=0.5|σz-σr|
(7)
由式(4)~(10)可得出接触硅片在弹性接触阶段的应力分布情况如图4所示。
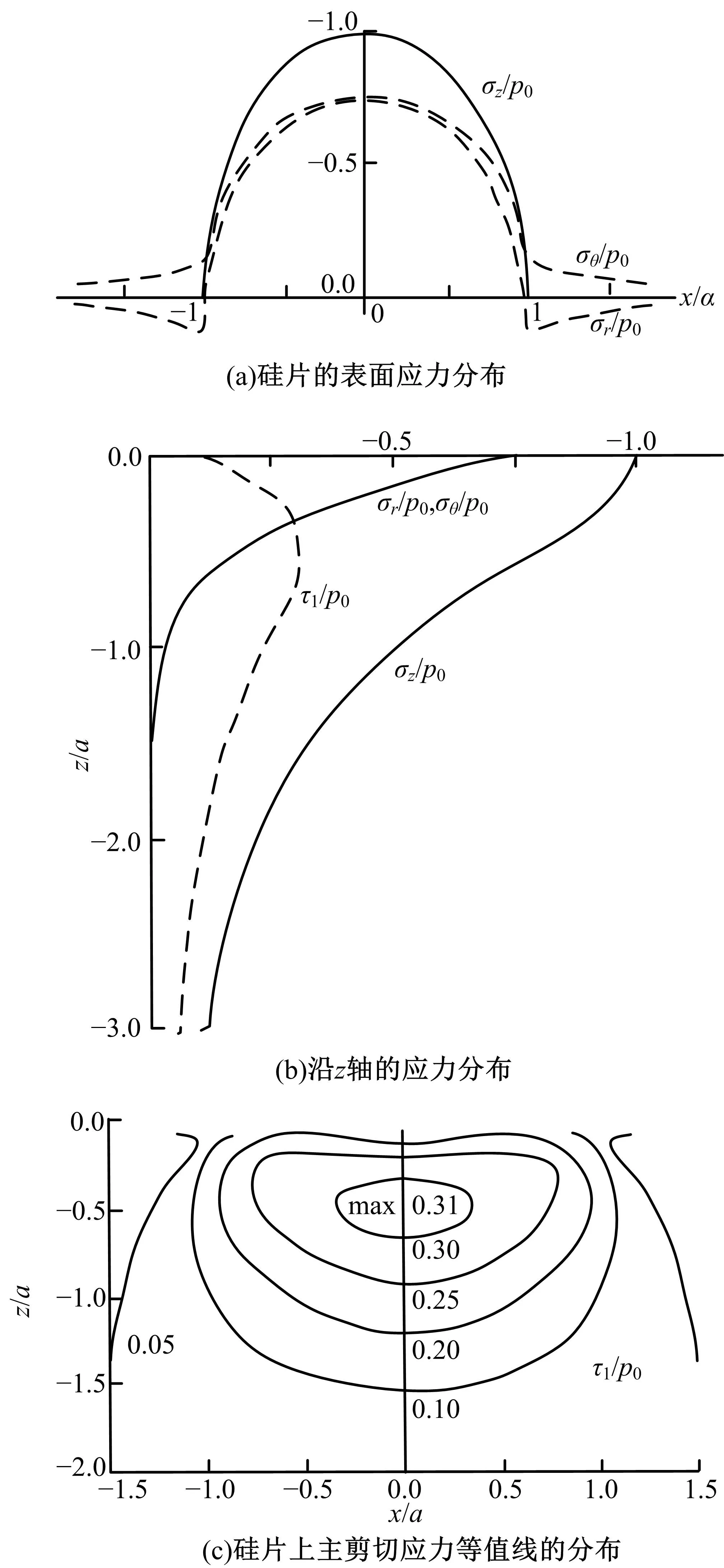
图4 弹性接触阶段接触硅片的应力分布Fig.4 Stress distribution of contact with silicon wafer during elastic contact phase
法向载荷反作用到砂轮微单元上可看成是以结合剂为基体、金刚石磨粒为表层的双层体受法向力作用的情形,如图5所示。根据多层体上的接触力学赫兹理论[9],可对砂轮微单元进行载荷应力分析。双层体接触力学分析过程中,设定表层的弹性模量E1对应砂轮微单元中金刚石磨粒的弹性模量ED,表层的厚度为h,对应磨粒的直径2R;基体的弹性模量E2对应砂轮微单元中结合剂的弹性模量EJ,接触半径为a。

图5 砂轮微单元受载荷看作双层体接触受力示意图Fig.5 Contact force diagram of wheel micro unit load as double body
根据双层体弹性接触理论分析结果给出不同E1/E2比值下砂轮微单元等效的应力分布情况,如图6所示。

图6 弹性接触阶段砂轮微单元等效应力分布Fig.6 Elastic contact stage grinding wheel micro unit equivalent stress distribution
由图6可以看出:砂轮微单元双层体在接触表面上的应力分布与作用在硅片接触表面的情况相似,只是方向相反,互为作用与反作用力,而接触表面以下由于是双层体,虽正应力分布的趋势仍与硅片上的相似,但由于存在界面,不同的材料特性(弹性模量及泊松比不同)使得剪应力的传递在界面上出现跳跃或不连续性。
2.2 法向塑性接触
分解的法向上,切深tw超过弹性临界切深后,接触开始进入塑性阶段,可根据接触力学[9]的“空腔模型”理论(见图7)来进行分析。硅片产生的内层位移近似成起始于接触点的放射线,它的应变等值线是半球形。在这个简化的塑性接触模型中,磨粒的接触面被包围在半径为a的半球“静水压力核”内,核内有平均接触压力pm,pm不会使硅片产生塑性屈服,但在“静水压力核”之外,塑性流动向周围扩散,塑性应变逐渐变小,直至半径为c处的弹性应变,这是塑性变形的边界,其中c>a。
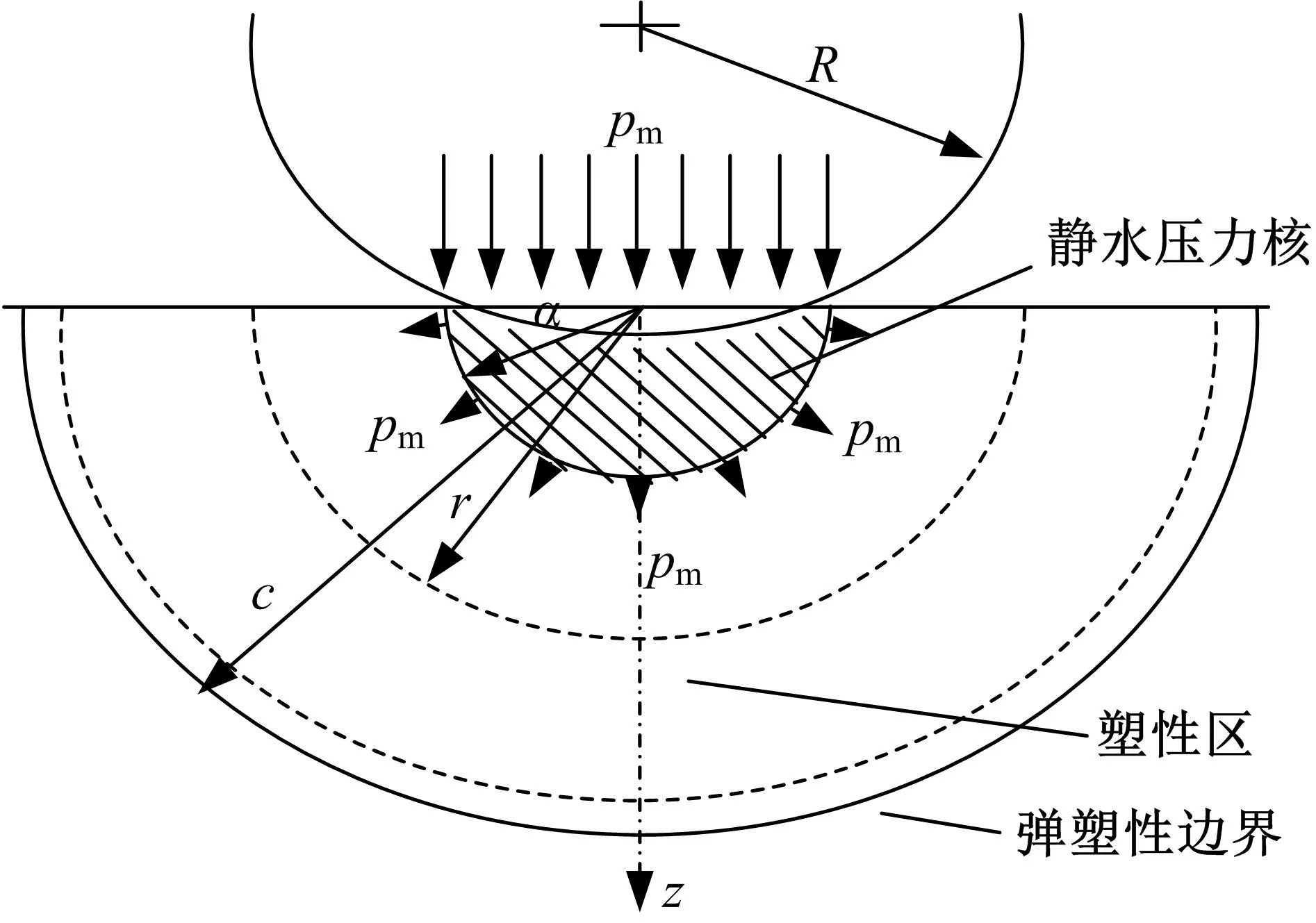
图7 塑性压入硅片的空腔模型示意图Fig.7 Schematic diagram of cavity model of plastic pressure in silicon wafer
在硅片塑性区a≤r≤c,应力表达式为:
(8)
在硅片弹性区r≥c,应力表达式为:
(9)
在静水压力核的边界上,pm可表达为:
(10)
而塑性变形边界位置的表达式为:
(11)
将式(11)代入式(10)可得半球核内压力表达式为:
(12)
分析式(12)可知,随着磨粒切入尺寸(a/R)的增大,硅片所受的平均压力也逐渐增大,同样法向载荷也随之增大,硅片也会从初始塑性变形逐渐扩展至塑性极限而出现断裂,即当球核内的最大应力达到硅片的脆性破裂强度时,就会出现裂纹。
将硅片的脆性破裂强度代入式(12)可得出对应精磨3000#砂轮(对应的磨粒半径R约为2 μm)的微单元与硅片塑性接触产生半球核半径a的临界值约1.1 μm,临界切深约330 nm,临界法向载荷约45 mN。与单颗金刚石磨粒的硅片压痕试验[10]结果(如图10所示,其压头曲率半径为2 μm)相吻合,也说明本文进行的微接触法向弹性及塑性理论分析是有效的。

图8 不同载荷下单晶硅单次压痕形貌图Fig.8 Monocrystalline silicon single indentation morphology under different load
硅片在受法向载荷作用处于塑性阶段时,砂轮微单元上的应力作用情况与硅片受法向载荷处弹性阶段的分析相似,砂轮微单元仍看作是双层体受载荷作用的情形,只是此阶段的法向载荷变大,由于金刚石磨粒的屈服强度极高,较难出现塑性变形,内部应力分布形式不会变化,只是应力数值会随之增大,结合界面上的剪应力同样会随之增大,这样出现界面破坏的可能性就更高。
2.3 叠加切向接触
宏观滑动摩擦定律为f=μFn,其中μ为滑动摩擦因数,它是与载荷、接触面积、滑动速度等条件无关的恒定量,而在微观滑动接触情况下,滑动摩擦因数就不再是恒定量,根据能量耗散机制,滑动摩擦力f可假设为滑动时剪切粘着点产生的粘着摩擦力fa和变形产生的形变摩擦力fd,即f=fa+fd,这样滑动摩擦因数μ也可看成是粘着摩擦因数μa和形变摩擦因数μd,即μ=μa+μd。 当接触切深较小时,处于弹性接触阶段,滑动摩擦力主要是由滑动中的粘着效应产生,根据粘着摩擦机理理论,粘着摩擦力为:
fa=μaFn=Azτa
(13)
式中:τa为硅片抗剪切强度平均值。
将式(1)(2)代入式(13),得到粘着摩擦因数为:
(14)
由式(14)可分析出,在弹性接触阶段,滑动摩擦力随着切深及法向载荷的增大是增大的,而其粘着摩擦因数是随之减小的。
切深越过弹性临界后,接触开始进入塑性阶段,此时滑动摩擦力主要是由犁沟形变产生,根据形变摩擦机理理论,形变摩擦力为fd=μdFn。
由塑性半球核模型知,核内有平均接触压力pm,故Fn=pmAz,fd=pmAx,可求得形变摩擦因数为:
(15)
由式(15)可分析出,在塑性接触阶段,滑动摩擦力随着切深及法向载荷的增大是增加的,其形变摩擦因数也是随之增大的。
求出切向上的滑动摩擦力,与法向载荷叠加合成后作用在硅片上,其合成载荷在硅片上产生的应力分布情况与法向载荷作用时相似,仍可采用弹性阶段赫兹理论与塑性阶段空腔模型理论来分析,只是载荷值有所增大,方向有所偏转,应力分布情况与单一法向载荷时类似,如图9所示。
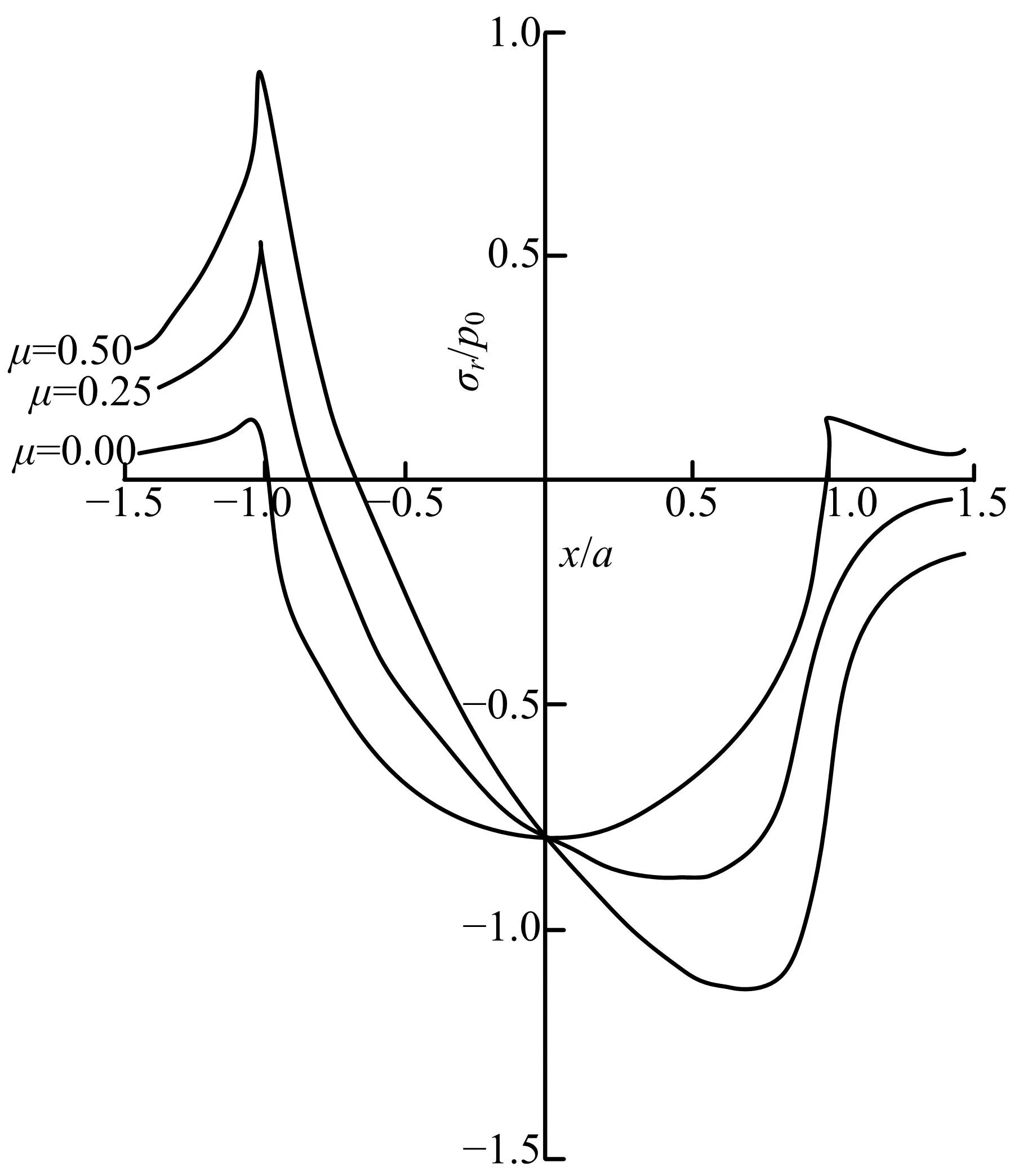
图9 叠加上切向滑动摩擦后硅片应力分布情况Fig.9 Stress distribution of silicon wafer after sliding friction is superimposed
滑动摩擦力作用在砂轮微单元上应力分布的情况与法向载荷作用时的分析相似,仍要把砂轮微单元看作双层体来分析。由于双层体的材料非均质性且存在界面,随着弹性模量比值及摩擦因数的增大,磨粒接触区域的前端出现最大压应力与后端出现最大拉应力的趋势更显著。不同弹性模量比时磨粒接触表面的应力分布如图10所示。
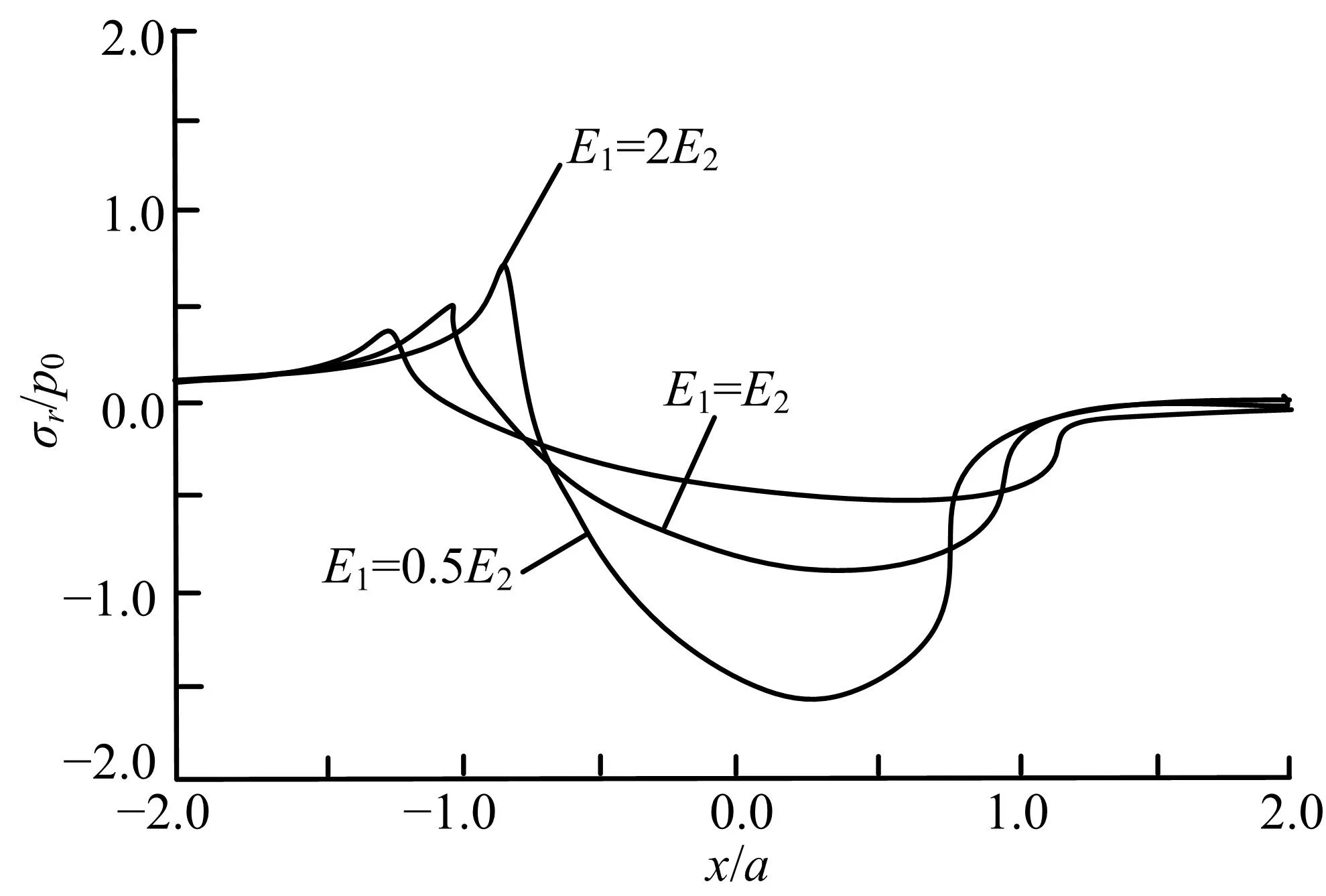
图10 叠加上切向滑动摩擦后磨粒上应力分布情况Fig.10 Stress distribution of grinding grain after tangential sliding friction is superimposed
分析结果与本文作者所做的微接触仿真分析[11]结果中切向滑动时硅片和砂轮微单元上的应力分布趋势相一致,如图11和图12所示,说明本文进行的微接触叠加切向的理论分析是有效的。

图11 硅片上切向滑动仿真的应力云图Fig.11 Stress diagram on silicon wafer during tangential sliding simulation
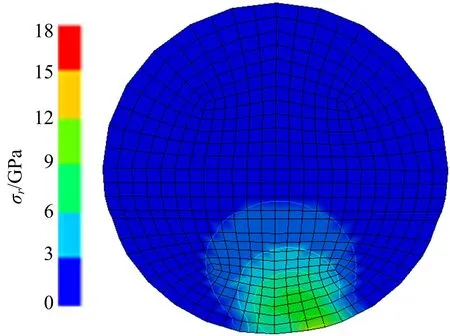
图12 切向滑动仿真砂轮微单元磨粒上的应力云图Fig.12 Stress diagram on grinding grain of wheel micro unit during tangential sliding simulation
3 结 论
(1)从硅片自旋转稳定延性域磨削过程中抽取出砂轮微单元与硅片的微接触作为研究对象,设定假设条件,提出并建立了微接触的理想三体力学模型。
(2)根据磨削过程,对力学模型中的接触力进行了分解,法向上运用接触力学中的赫兹理论与“空腔模型”理论,将分析获得了硅片上对应弹性和塑性阶段的载荷及应力分布情况,同时也获得了砂轮微单元上相应的应力分布情况。将分析结果与单颗粒金刚石硅片压痕试验结果进行对比,证明分析方法有效。
(3)切向上运用微观摩擦学理论分析得出了滑动摩擦力,叠加合成法向载荷后获得了微接触过程中硅片与砂轮微单元上的应力分布情况。将分析结果与砂轮微单元微接触硅片的仿真结果进行对比,证明分析方法有效。本文的研究结果可对研究硅片自旋转磨削机理提供相关理论支撑。
参考文献:
[1] Markku T, Teruaki M, Veli-Matti A, et al. Handbook of Silicon based MEMS Materials and Technologies[M]. 2nd ed. London:William Andrew,2015.
[2] Pei Z J, Strasbaugh A. Fine grinding of silicon wafers[J]. International Journal of Machine Tools and Manufacture,2001,41(5):659-672.
[3] Matsui S. An experimental study on the grinding of silicon wafer-the wafer rotation grinding method[J]. Bull Japan Soc Prec Eng,1988,22(4):295-300.
[4] Zhou L,Tian Y B,Huang H,et al. A study on the diamond grinding of ultra-thin silicon wafers[J]. Journal of Engineering Manufacture,2012,226(1):66-75.
[5] Pei Z J,Fisher G R, Milind B, et al. A grinding-based manufacturing method for silicon wafers: an experimental investigation[J]. International Journal of Machine Tools & Manufacture,2005,45(10):1140-1151.
[6] 康仁科,田业冰,郭东明,等. 大直径硅片超精密磨削技术的研究与应用现状[J]. 金刚石与磨料磨具工程,2003,136(4):13-18.
Kang Ren-ke,Tian Ye-bing,Guo Dong-ming, et al. Present status of research and application in ultra-precision grinding technology of large-scale silicon wafers[J]. Diamond & Abrasives Engineering,2003,136(4):13-18.
[7] Yan J W,Tooru A,Hirofumi H,et al. Fundamental inverstigation of subsurface damage in single crystalline silicon caused by diamond machining[J]. Precision Engineering,2009,33:378-386.
[8] 霍凤伟. 硅片延性域磨削机理研究[D]. 大连:大连理工大学机械工程学院,2006.
Huo Feng-wei. Study on the mechanism of ductile mode grinding of silicon wafers[D]. Dalian: School of Mechanical Engineering, Dalian University of Technology,2006.
[9] Johnson K L. Contact Mechanics[M]. London:Cambridge University Press,1985.
[10] 张赜文. 单压头曲率半径对单晶硅和氮化碳薄膜径向纳动损伤的影响[D]. 成都:西南交通大学机械工程学院,2010.
Zhang Ze-wen. Effect of equivalent radius of indenter on the radial nanofretting damage of monocrystal silicon and α-CNxfilm[D]. Chengdu: School of Mechanical Engineering,Southwest Jiaotong University,2010.
[11] 任庆磊,魏昕,谢小柱,等. 硅片自旋转磨削中基于作用力的微观接触仿真研究[J]. 金刚石与磨料磨具工程,2016,36(2):19-23.
Ren Qing-lei,Wei Xin,Xie Xiao-zhu, et al. Simulation of micro contact based on interacting force in self rotating grinding of silicon wafer[J]. Diamond & Abrasives Engineering,2016,36(2):19-23.